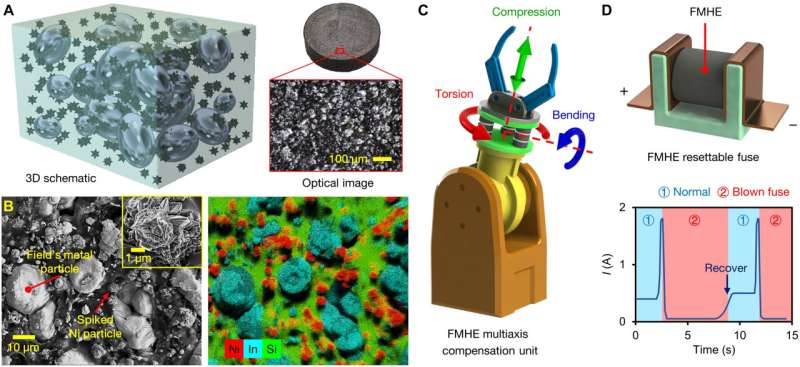
Smart materials are materials that have the ability to change their properties in response to specific external stimuli, such as temperature, humidity, light, or applied stress. One of the most well-known examples of smart materials is shape memory alloy (SMA), which is a type of metallic material that can change its shape in response to changes in temperature.
Another example of smart materials includes piezoelectric materials, which generate an electric charge in response to applied mechanical stress. Smart materials have a wide range of potential applications, including in aerospace, automotive, robotics, manufacturing, and biomedical engineering.
Variable stiffness materials are a type of smart materials that have the ability to tune their stiffness, or resistance to deformation, in response to external stimuli. This property allows for the material to adapt to changing conditions and improve performance in a wide range of environments.
One of the main advantages of variable stiffness materials is that they can increase the efficiency, safety, and reliability of mechanical systems. For example, variable stiffness materials can be used to create robotic arms and grippers that can adapt to different objects and environments. This allows for the robotic arm or gripper to handle a range of different objects with different shapes, sizes, and weights, which can reduce the complexity and increase the overall efficiency of the robotic system.
Innovative smart materials with tuneable electromechanical properties are revolutionizing the fields of manufacturing, wearable devices, and robotics. However, to date, a material that can intelligently self-tune its electrical and mechanical properties in response to environmental changes, and harness the altered properties synergistically without external control, has yet to be achieved.
To fill this gap, a collaborative research team led by Dr. Shiyang Tang at the University of Birmingham, along with collaborators from the University of Science and Technology of China, the University of Cambridge, and the University of Wollongong, developed a smart material called the Field’s metal hybrid filler elastomer (FMHE). The FMHE comprises hybrid fillers of Field’s metal (a non-toxic low-melting-point alloy) and spiked nickel microparticles embedded in an elastomer matrix.
This research was reported in their recent paper published in Science Advances.
The FMHE created by the researchers can respond to both mechanical strain and electrical currents, exhibiting variable and tuneable electrical conductivity and stiffness without external control. The melting and solidification of the Field’s metal enable the change in stiffness. The FMHE also exhibits unconventional negative piezoresistivity and high strain sensitivity, with resistivity decreasing millions of times upon both compression and stretching.
By harnessing these properties in a synergistic manner, the researchers demonstrated two applications in intelligent and resilient systems, with over an order of magnitude performance improvement compared to the state-of-the-art. The first application is a self-triggered multi-axis compliance compensator that can protect robotic manipulators from excessive compressive, bending, and torsional movements.
The second application is a resettable current-limiting fuse that offers adjustable fusing currents and significantly outperforms commercial products in terms of compactness, range of operating current, and response speed.
“I am thrilled that our experiments and simulations have uncovered the mechanism behind the negative piezoresistive effect and the tuneable conductivity, strain sensitivity, and stiffness of this smart material. I hope this research is the beginning of the further study on this new material family, which has the potential to revolutionize the development of intelligent and resilient robotics and electronics,” said Dr. Guolin Yun, the first author of the study.
“These self-responsive smart materials not only offer cost-saving opportunities but also increase reliability by reducing the need for complex control systems,” said Dr. Shiyang Tang.
This study provides significant value to the fields of manufacturing, robotics, and electronics, potentially leading to the development of electromechanical systems with enhanced performance and functionality.
More information: Guolin Yun et al, Electro-mechano responsive elastomers with self-tunable conductivity and stiffness, Science Advances (2023). DOI: 10.1126/sciadv.adf1141
Journal information: Science Advances
Provided by University of Birmingham