by Martha Höhne, Leibniz Institute for Catalysis
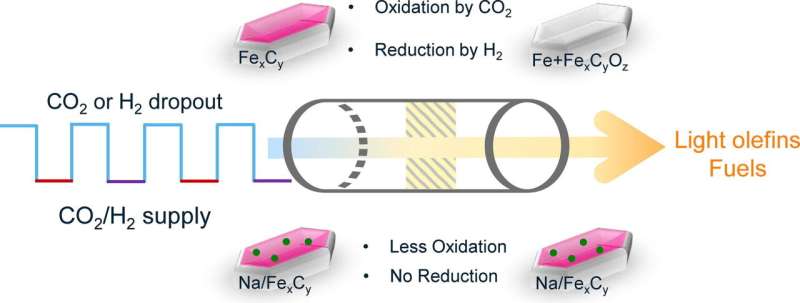
Wouldn’t it be an elegant solution to use the substance that is most damaging to the climate and threatens the future as a raw material for economic goods and everyday items? In fact, carbon dioxide (CO2), an unavoidable byproduct of civilization, is already being used in the laboratory to produce lower olefins, alcohols and fuels in combination with hydrogen and other chemical reactants, all of which can be obtained sustainably. For such processes to become industrial practice, they must be able to run under “fluctuating” conditions.
“Fluctuating” means that these processes must also function with fluctuating supplies of energy and starting materials. This is new for chemistry, but cannot be avoided if the energy, for example for the production of hydrogen by electrolysis, is to come from renewable sources such as sun and wind in the future. These are not available continuously and not at all on windless nights.
However, the influence of dynamic conditions on chemical reactions has hardly been studied so far, as Prof. Dr. Angelika Brückner and Prof. Dr. Evgenii Kondratenko at the Rostock Leibniz Institute for Catalysis explain. Their research group is involved with work on developing catalysts for CO2 hydrogenation to higher hydrocarbons under fluctuating conditions.
From climate gas to raw material
In the grand scheme of things, the goal is to replace petroleum as a raw material base and at the same time to ennoble a problematic waste gas, carbon dioxide, into a raw material. But CO2 is an inert gas and hardly reacts on its own.
To obtain commercially useful compounds, especially basic materials for the chemical synthesis of valuable products, the extremely stable carbon-oxygen bonds in CO2 must be activated. This is done catalytically by hydrogenation, i.e., hydrogen is added, which can produce a variety of different hydrocarbon compounds. The more carbon atoms they contain in the molecule, the higher their valence.
For the process, the chemists modified the so-called Fischer-Tropsch synthesis, which was developed almost a hundred years ago for the hydrogenation of carbon monoxide (CO). To do this, they replaced the highly toxic CO with CO2.
Iron catalyst changes
The structure and properties of the catalyst play a key role in determining which products are formed during CO2 hydrogenation. In the case of Brückner and Kondratenko, it is an iron catalyst. But not all iron is the same, they say. They discovered that the catalyst changes in the reaction under fluctuating conditions: It keeps forming new “phases and species” in between, they say.
To precisely distinguish between favorable and obstructive phases, the researchers observe the catalyst at work, so to speak. This is done using highly specific operando-spectroscopic analysis methods based on infrared, UV and laser light. The catalyst samples are partly developed by the researchers themselves and partly obtained from their research partner at the Humboldt University in Berlin.
Catalytically, iron is often used in the form of oxides, explains Prof. Kondratenko. “But we prefer to obtain methane with it.” With the molecular formula CH4, methane is the main component in natural gas and the simplest hydrocarbon. “However, we are after higher-value hydrocarbons, currently, for example, olefins.” These are indispensable basic chemicals that can be further refined chemically.
Active catalytic phase: Iron carbide
The Rostock scientists discovered that one phase in particular is crucial for CO2 hydrogenation, in which iron carbide is formed at the catalyst surface. And they learned how to stabilize this carbide phase and avoid the interfering phases. For example, by using iron oxalate, an iron salt of oxalic acid (FeC2O4), instead of the usual iron oxide as the catalyst material. The team recently published two articles on this topic in Catalysis Science & Technology and the Journal of Catalysis.
A third publication of the group, in ACS Catalysis, reports on the problem of the decreasing activity of the iron catalyst. As a cause, the Rostock chemists discovered intermediates that convert to coke under certain circumstances. This is deposited as a tough layer on the catalyst surface and obscures the active species.
For future plants, the vision would be to convert the carbon dioxide right where it accumulates en masse and use it as a raw material, say Prof. Dr. Brückner and Prof. Dr. Kondratenko. In accordance with the principles of green chemistry and the circular economy, such a process would be particularly suitable in the environment of the currently largest CO2 emitters, such as the cement industry, iron and steel production and the chemical industry itself, where the CO2 can be further processed with “green” hydrogen into valuable hydrocarbons.
More information: Qingxin Yang et al, The role of Na for efficient CO2 hydrogenation to higher hydrocarbons over Fe-based catalysts under externally forced dynamic conditions, Journal of Catalysis (2023). DOI: 10.1016/j.jcat.2023.07.012
Andrey S. Skrypnik et al, Spatial analysis of CO2 hydrogenation to higher hydrocarbons over alkali-metal promoted iron(ii)oxalate-derived catalysts, Catalysis Science & Technology (2023). DOI: 10.1039/D3CY00143A
Qingxin Yang et al, Understanding of the Fate of α-Fe2O3 in CO2 Hydrogenation through Combined Time-Resolved In Situ Characterization and Microkinetic Analysis, ACS Catalysis (2023). DOI: 10.1021/acscatal.3c01340
Journal information: ACS Catalysis
Provided by Leibniz Institute for Catalysis